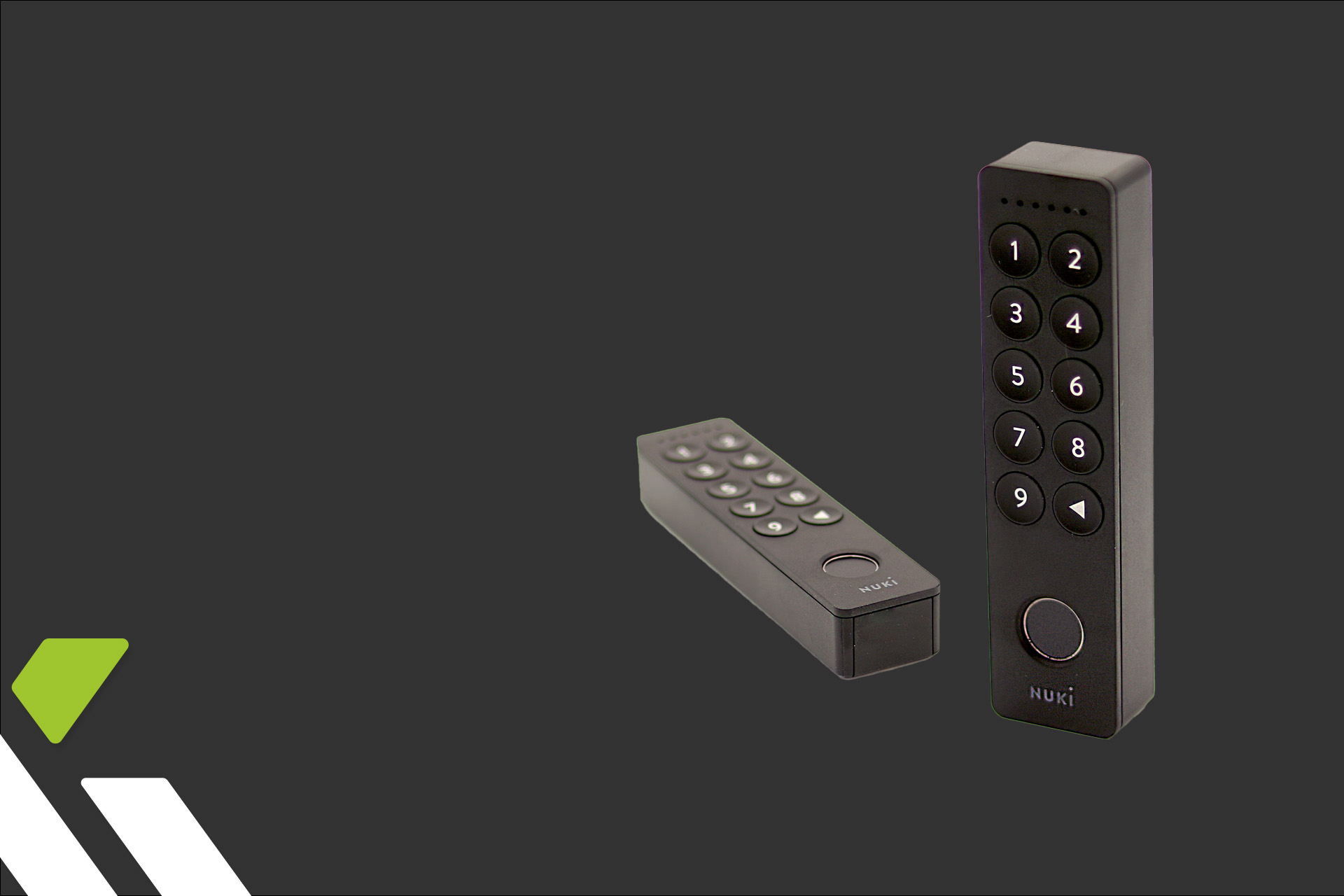
Einblicke in die Entwicklung: das Keypad 2.0 von Nuki
Vom ersten Konzept bis zum fertigen Premium-Produkt für Endkund:innen: Die Nuki Home Solutions GmbH mit Sitz in Graz ist Pionier und europäischer Marktführer bei Smart Locks. Mit dem elektronischen Türschloss gehört der physische Schlüssel der Vergangenheit an, man kann fortan mit einer Sorge weniger durch’s Leben gehen und hat dennoch seine Tür jederzeit im Griff – gutes Gewissen, volle Kontrolle und zertifizierte Sicherheit inklusive. Mit dem neuen Keypad 2.0 öffnet man nun seine Tür so schnell wie noch nie: ganz einfach mit dem Finger.
Das Keypad 2.0 ist somit das perfekte Zubehör für das Nuki Smart Lock. Darüber hinaus bietet das Keypad 2.0 für Kund:innen eine einfache Installation und eine hohe Benutzerfreundlichkeit. Durch den Einsatz der Fingerprint-Technologie oder durch Eingabe eines 6-stelligen Zutrittscodes öffnet man seine Tür innerhalb weniger Sekunden. Das Nuki Keypad 2.0 ist seit November 2022 auf dem Markt erhältlich. Das hochwertige Endprodukt, das Kund:innen nun in Händen halten können, ist das Ergebnis einer tollen Zusammenarbeit und einer erfolgreichen Projektumsetzung zwischen uns und der Nuki Home Solutions GmbH.
Alles begann mit einer ersten Anfrage zur Entwicklung eines Keypads an uns. Im Vordergrund standen die Premium-Qualität sowie die hohe Funktionsfähigkeit des neuen Produktes. Kund:innen sollten durch die Ästhetik und Haptik sofort die Hochwertigkeit und Präzision des Produktes wahrnehmen können. Ein durchdachter Kern und die smarte Technologie sollen mit einer angenehmen Haptik eine ansprechende und moderne Form ergeben. Schließlich muss das Produkt, an der Außenfassade angebracht, nicht nur optisch, sondern auch funktionell überzeugen. Mit den ersten Auftragsspezifikationen ging es nach einer Aufwandseinschätzung in die grundlegende Konzeptionsphase über. Hier ist es uns besonders wichtig, bereits im ersten Schritt den Kunden möglichst transparent und übersichtlich in die Projektumsetzung zu involvieren. Eine laufende Abstimmung mit Nuki war daher eine wichtige Grundlage für eine gelungene Umsetzung des Keypads 2.0.
In der Prototypen-Herstellung setzten wir auf unsere hausinterne Fertigungstechnologien im Bereich 3D-Druck, um die Produktion der einzelnen Bauteile zu perfektionieren. Die Phase des Prototypings erlaubte es, die Funktionsfähigkeit des Produktes zu überprüfen und gegebenenfalls anzupassen. Hauptaugenmerk liegt dabei stets auf dem Zusammenspiel der einzelnen Bauteile und der Entwicklung eines geeigneten Herstellungsprozesses für unsere Kunden, in diesem Fall für die besonderen Anforderungen des Keypads 2.0. Hier herrschten beispielsweise sehr enge Platzverhältnisse vor, die eine umfangreiche Funktionsfähigkeit auf wenig Bauraum erforderten. Das stellte nicht nur für die Bauteilauslegung, sondern auch für das Toleranzmanagement eine Herausforderung dar.
Nach einer erfolgreichen Konzeptionsphase wurde gemeinsam mit Nuki die Planung der Serienproduktion eingeleitet. Das Seriendesign beinhaltete Kunststoff-Spritzgussteile, Stanzteile und Stanz-Biegeteile sowie einen Silikonguss. Jedes Bauteil durchlief eine Fehlermöglichkeits- und Einflussanalyse, um die spezifischen Bauteilanforderungen festzulegen und ein finales Konzept für den Zusammenbau zu entwickeln. In einer sogenannten DFM-Phase („Design for manufacturing“) ging es in weiterer Folge um eine konkrete Abstimmung mit den Bauteil-Lieferanten, bevor eine Serienproduktion in die Wege geleitet werden konnte. In einer Erstbemusterung der Bauteile sowie durch eine Funktionsprüfung wurden alle Eigenschaften gründlich untersucht: Beispielsweise das Einrasten des Montageplatte-Schnappers, die Druckpunkte der Knöpfe oder das Öffnen des Batteriedeckels wurden hierbei genau unter die Lupe genommen. Ein weiterer, wesentlicher Faktor war die „Schutzklasse IP54“ – das Keypad 2.0 muss gegen Spritzwasser geschützt sein und gewährleisten, dass es vollkommen staubdicht bleibt. Eigenschaften, die wir durch laufende Testungen und Verbesserungen möglich gemacht haben. Um die hohe Produktqualität des Keypads 2.0 sicherzustellen, gab es auch in dieser Phase Änderungsschleifen sowie eine erneute Bemusterung der Bauteile. Erst als alle Anforderungen erfüllt waren, starteten wir die Vorserie mit einem Zusammenbau durch einen Lohnfertiger. Darauf folgten erneute Testläufe mit dem fertig zusammengebauten Keypad 2.0. Darunter beispielsweise ein Droptest aus 1,2m Höhe, eine Dichtheitsprüfung auf IP54, Testungen im Klimaschrank oder die Lebensdauertestung der Buttons.
Aus den Ergebnissen dieser Testungen konnten wir ein präzises Maßnahmenpaket erstellen, um die Bauteile in verbesserter Form in die Vorserie zu bringen. Mit dem Abschluss der erfolgreichen Vorserien-Phase wurde das Nuki Keypad 2.0 für die finale Serienproduktion freigegeben. Das Nuki Keypad 2.0 ist seit Ende 2022 offiziell gelauncht – und wir dürfen auf eine erfolgreiche Projektumsetzung zurückschauen.