Making ideas tangible
3D printing
Additive manufacturing or 3D printing has long been pushing the boundaries of traditional manufacturing processes. It ensures cost reduction and fast results in product development and in the manufacturing process of small series.
Making ideas tangible
3D printing
Additive manufacturing or 3D printing has long been pushing the boundaries of traditional manufacturing processes. It ensures cost reduction and fast results in product development and in the manufacturing process of small series.
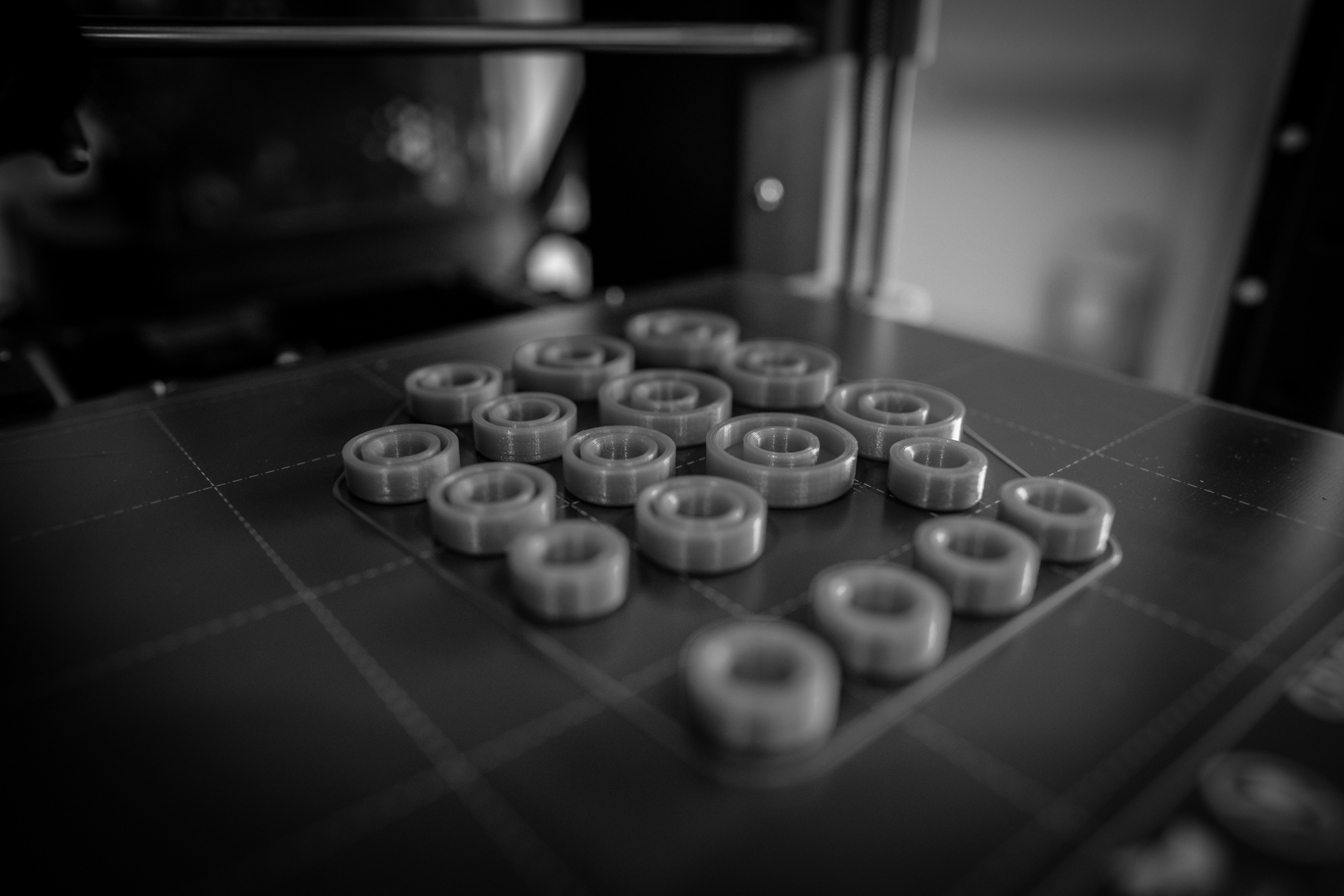
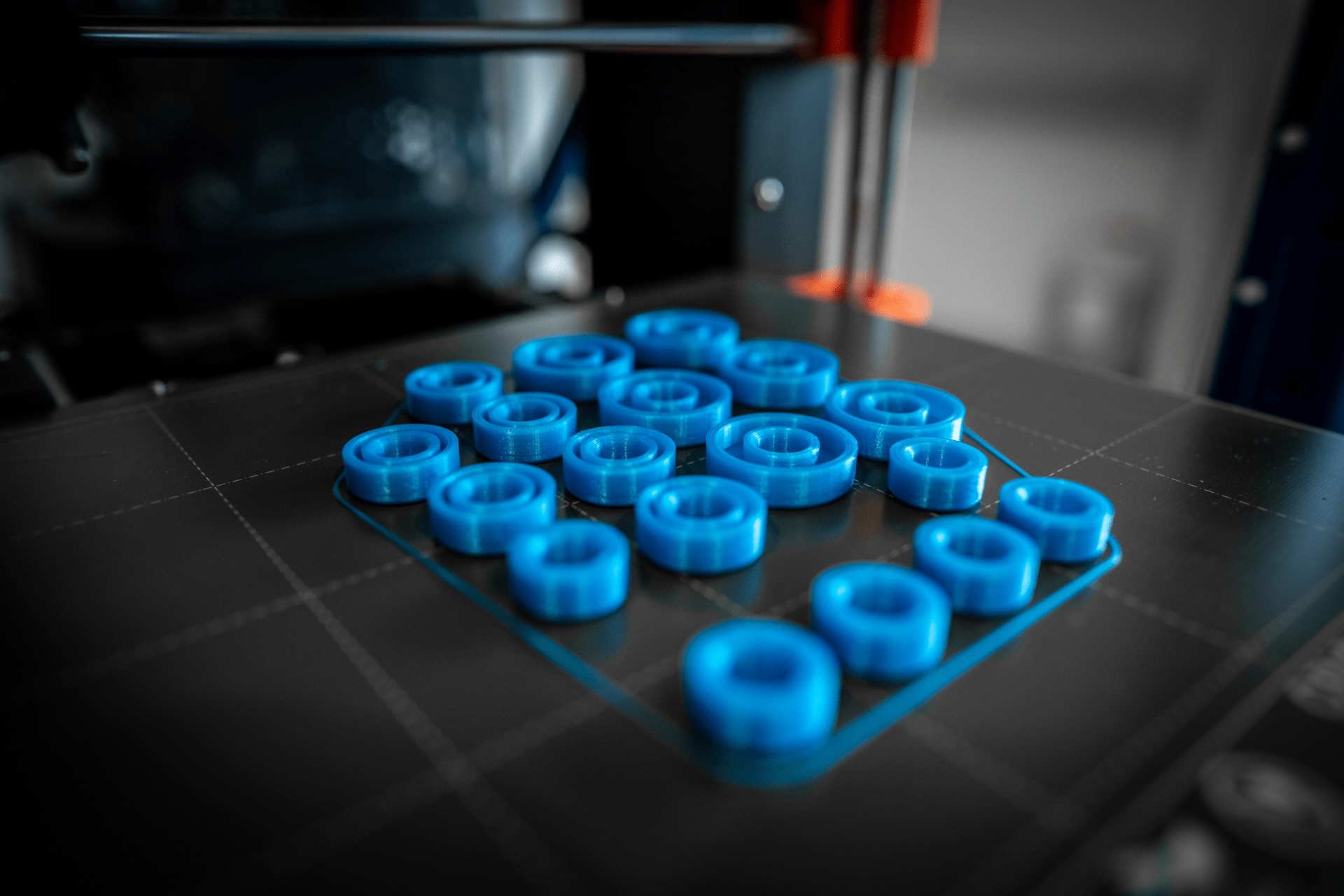
Initial consultation | Offer | Full transparency | Project management | Project completion | Ongoing support
We look forward to new challenges! Getting to know you personally is our top priority, so that we can pick you up at the right place with your idea. Once the goals and non-goals of the project have been clearly defined, we package your requirements in a transparent offer. It is important to us that you always find your individual requirements reflected in our implementation recommendation. In this way, we lay the important foundation for successful cooperation and subsequent project implementation.
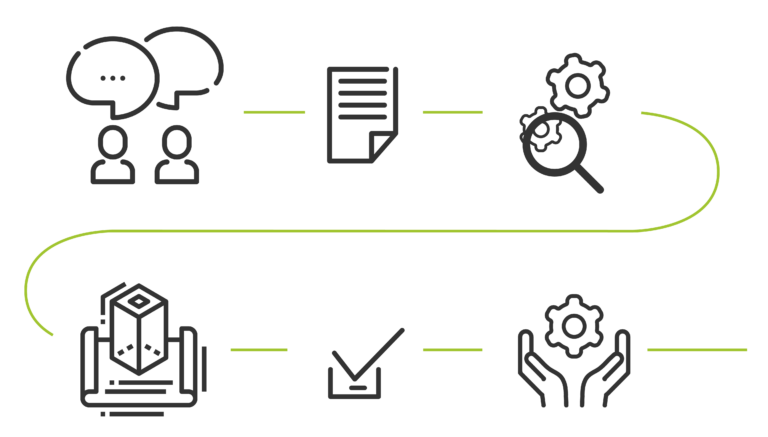
Additive manufacturing
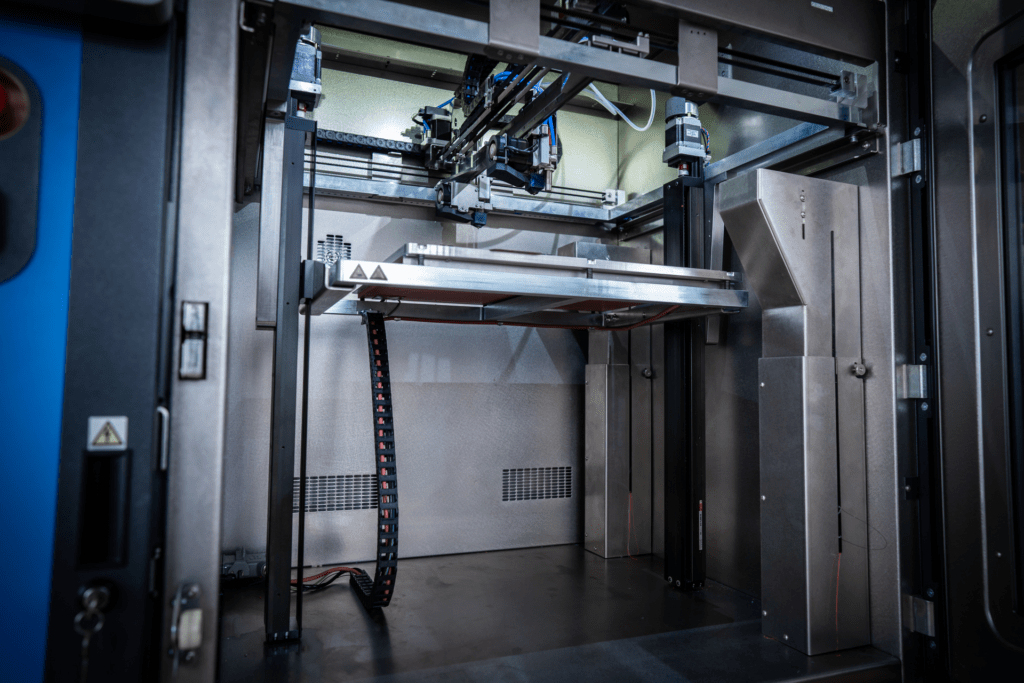
Prototypes | Small series production | Special machine construction
Highly complex geometries can be produced using additive manufacturing processes. The choice of the right manufacturing process depends on the respective component requirements, such as geometric complexity, strength, surface quality or dimensional accuracy. We candraw on technologies such as FDM – Fused Deposition Modeling, SLA– Stereolithography and SLS – Selective Laser Sintering .
A wide range of available engineering plastics enables XITEC to manufacture components with the right properties according to individual requirements.
3D printing process in detail
3D printing is a method of additive manufacturing. For you and your product, 3D printing as an additive manufacturing method means shorter product development times and a faster time to enter the market. You save resources and tools. This production solution allows you to work particularly accurately and, in addition to maximum precision, gives you comprehensive design freedom for your end products.
The FDM process (Fused Deposition Modeling) or the FFF process (Fused Filament Fabrication) is also known as fused layering or nozzle melting. It is one of the most common processes in the 3D printing sector and was developed by Scott Crump at the end of the 1980s. Your selected plastic filament (ABS or PLA are popular, for example) is melted and applied in layers to a print bed using an extruder. Which nozzle is used for application depends on the material selected for your object. The material also determines, among other things, the temperatures of the nozzle, the print bed and the installation space, as well as the speed at which the material is extruded.
The great advantage of this process is the wide choice of materials. The right plastic for your object can be found for a wide range of properties, such as temperature and UV resistance or stability requirements. The FDM or FFF process is therefore particularly suitable for the production of individual pieces or small batches, such as for the manufacture of tools, parts for automation technology or mechanical engineering, as well as for the construction of prototypes, devices or design objects.
In the SLA process(stereolithography process) or the DLP process (digital light processing process) , your object is created using light technology inside a tank filled with liquid synthetic resin (photopolymer). Both processes are used very frequently in 3D printing, although the SLA process can work a little more finely than the DLP process. The light sources differ; for example, we work with a laser in the SLA process and with an LCD display or DLP projector in the DLP process. The process using a synthetic resin tank is the origin of 3D printing methods and, through continuous further development, has become a cost-effective way of producing highly accurate, isotropic and waterproof prototypes and end-use parts.
In the SLA process, the individual layers are projected into the pool using a laser and allow the synthetic resin to solidify in the desired places. This creates an object whose structures can be designed even more finely than with the FDM process. This high print quality is particularly suitable for functional prototypes, models, molds and tools, and is flexible enough to meet the exact requirements of industries ranging from medicine to jewelry design. SLA resin formulations therefore cover a broad spectrum of optical, mechanical and thermal properties.
After the liquid synthetic resin has been transformed into a hardened plastic object, the material is still soft and unstable, which is why a support structure is also printed in these two processes. The fine supports are only removed after cleaning in a car wash and curing. For this purpose, your object is irradiated all around with UV light in a curing oven to achieve its final strength. The hardening temperatures and dwell times for the individual models vary depending on the properties and requirements.
In the SLS process (selective laser sintering), your object is created using powder and energy, without any binding agents. The energy source is a laser that “selectively” processes the component or prototype from a powdered plastic according to your CAD file.
This allows precise production, which, unlike the SLA process, is possible without additional support structures. This means that even almost impossible 3D printing results can be produced effortlessly. The extremely fine material powder is applied layer by layer using a roller and then fused locally with a laser beam.
This makes it possible to achieve particularly even, smooth surfaces. It is important that this process is followed by slow and continuous cooling in order to counteract potential deformation. In the final production step, the last powder residues are removed using sand and glass beads in a cleaning station.
Are you already familiar with our practical online store for 3D printing?
Click here for our service VOXL
Construction
Development | 3D Design | Detailed Drawings
We create the design data for components, assemblies or entire products from your idea. With our expertise as product developers, we support you in all areas of your development. No matter whether you need trade fair prototypes, customized orthopaedic products or the implementation of your product idea.
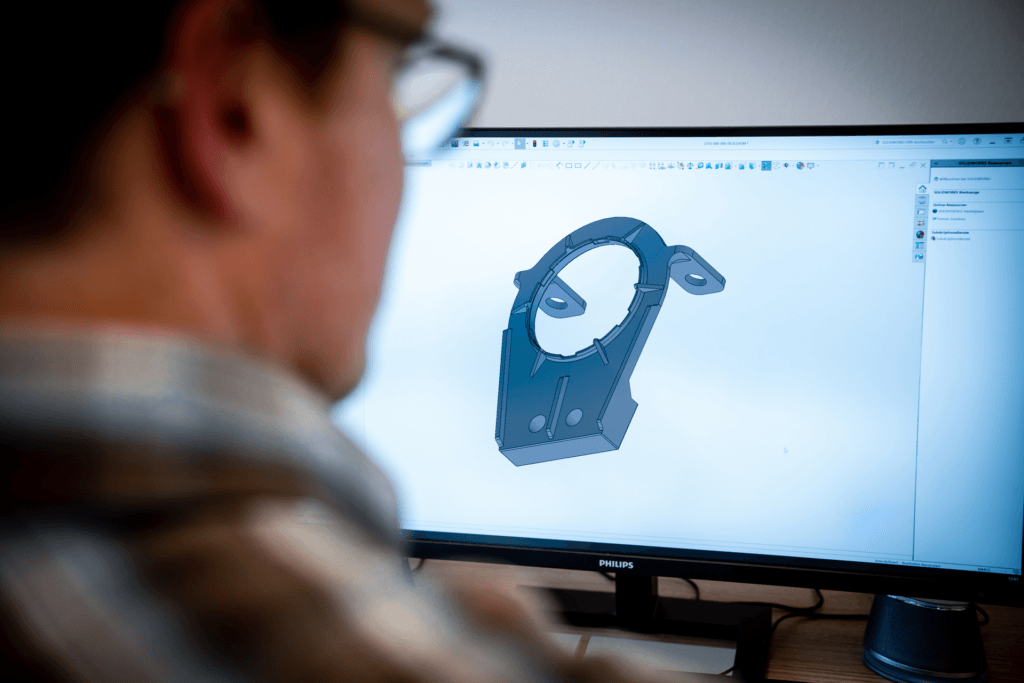
Finishings
In 3D printing, finishing or post-processing refers to the various downstream treatment techniques that help to refine or completely smooth out the layered appearance typical of 3D printing. It offers you the opportunity to optimize your components through post-processing so that, in addition to an elegant appearance, the stability or temperature resistance is also improved, for example. The finishes for the different surfaces vary depending on the 3D printing process selected. The texture is modified either by chemical smoothing, painting, coloring, coating or vibratory finishing. Find out more about the individual finishings here.
Blasting refines objects after completion of the SLS process. All components produced using the SLS process are sandblasted after an initial rough cleaning by hand brushing. The component is placed in a booth in which special blasting balls carefully remove the excess powder residue.
Nano-Seal is a finishing for objects created using the FDM process or the SLS process. The coating is temperature-resistant up to 180 °C. Liquid impregnating agent is applied to the component by brushing or dipping. The fine particles of the Nano-Seal particles are deposited in the pores of the material, giving the object an airtight and waterproof property.
Coloring is particularly suitable for components that need to be clearly differentiated by color. We are currently in the process of setting up this service for you. Coloring is suitable for nylon components using the SLS process. These include, for example, the plastics PA12, PA12GF or PA11. The selected dye then penetrates the material through a dye bath and colors the entire object. The color intensity depends on the base color of the selected material. The lighter the plastic, the clearer the coloration.
Topology optimization
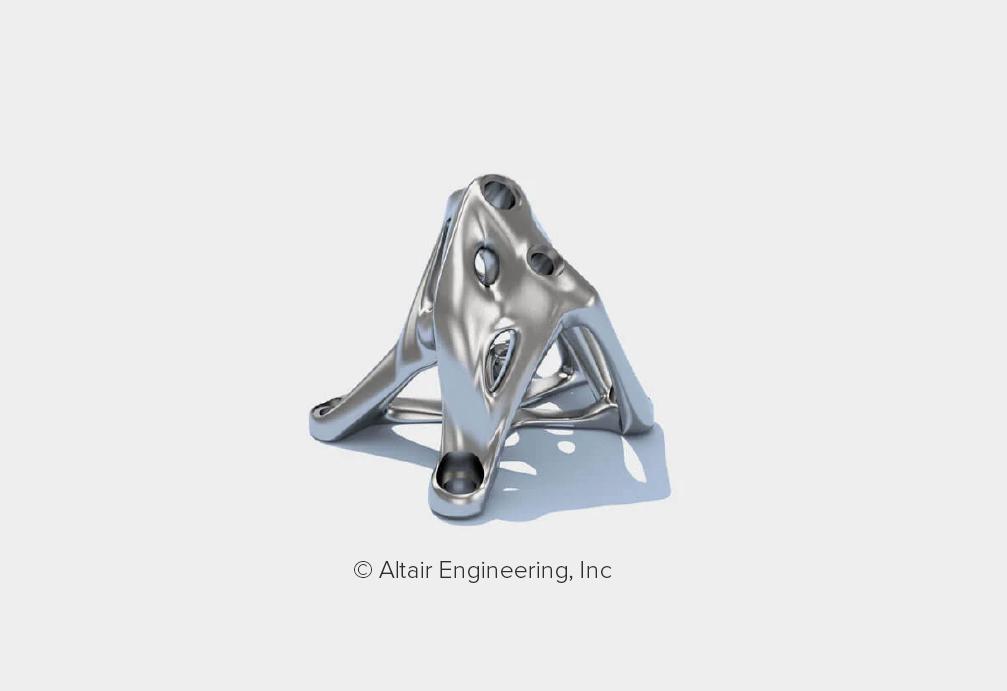
Cost reduction | Weight reduction | Mechanical load capacity | Geometry optimization
Topology optimization of design data creates geometric shapes that would be unthinkable to produce using conventional methods. A simulation is used to calculate an optimized component shape that aims to increase rigidity and reduce weight. The production of such optimized component geometries using additive technologies opens up completely new possibilities for you.
Ongoing support
Customer Support | Contact | Exchange
As a full-service partner, ongoing support is simply part of our package.
Technical products are constantly evolving, which is why we support you in the ongoing development of your project.
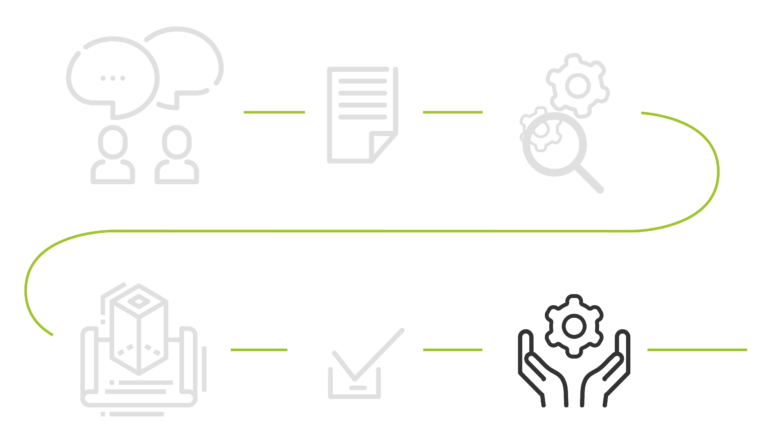