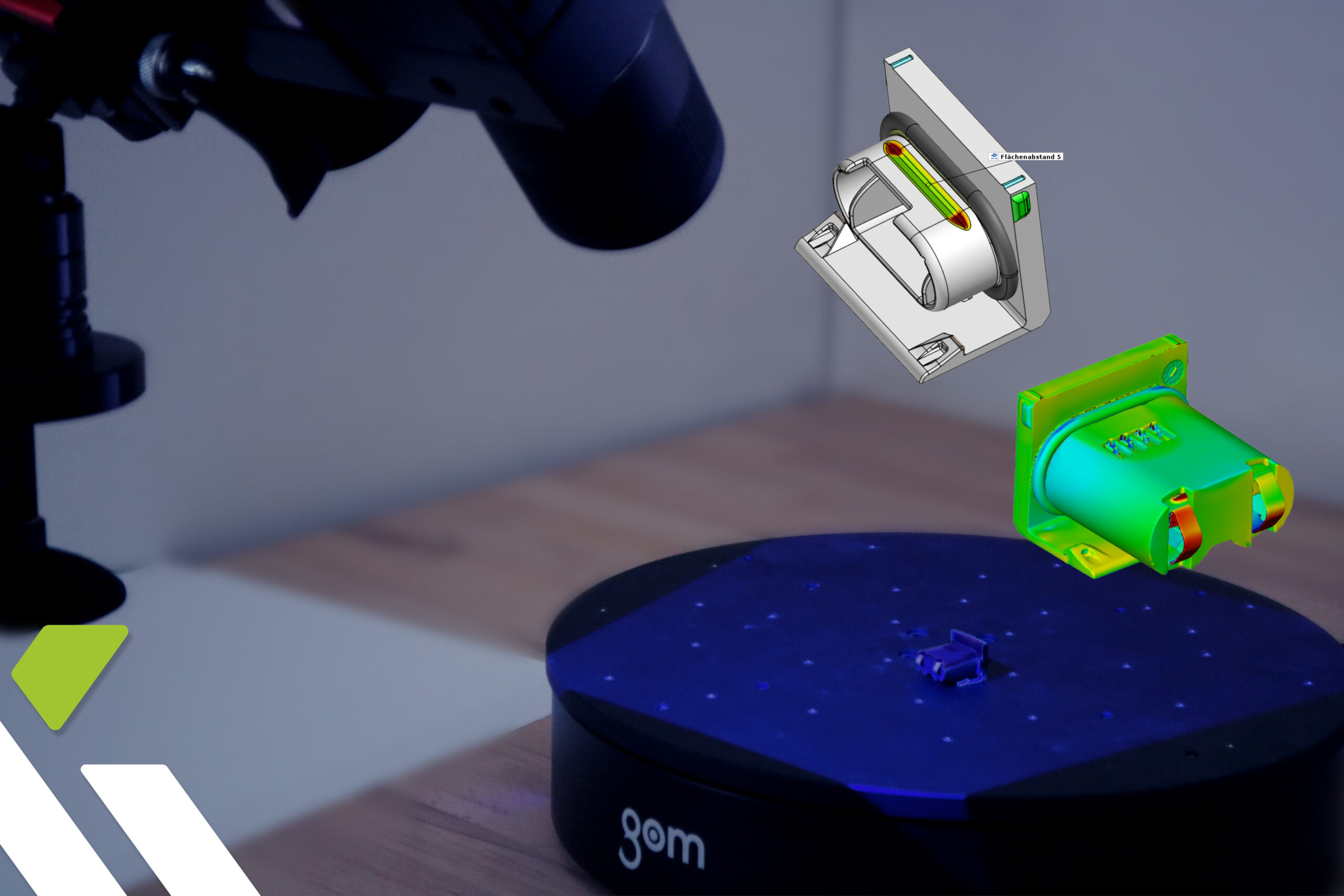
Digital assembly: Highest precision in assembly testing thanks to 3D metrology
Ourshe 3D Metrology service can do even more!
The design and precision in the production of components and assemblies play a decisive role in the functionality of technical products. Even a tiny error can lead to considerable problems. Methods therefore had to be developed to detect and compensate for any production errors in advance. We offer our customers one of these innovative methods for checking components and entire assemblies in our “3D Metrology” service. Using the latest measurement technology and a great deal of expertise, we scan and analyze components and their assembly almost in the blink of an eye.
In assembly testing, the challenge is to check the relative position of the components to each other with the utmost precision. This is crucial to ensure that the mechanics work properly. Minor deviations are detected in advance to prevent subsequent malfunctions. First, the individual components are scanned using our high-precision optical measuring device. The scanner uses Zeiss Blue Light Technology to capture the entire surface of the respective components. Comprehensive 3D models are created by polygonizing a point cloud. The individual components are then joined together to form an assembly in order to scan the entire group again. This time, however, the scans are only carried out at a few selected reference points. This additional scan is a great benefit for our customers: The wealth of information allows us to combine the individual scans with the group scan in order to analyze the interaction with pinpoint accuracy. Once this digital assembly has been created, the evaluation of all data begins. The various parameters are taken into account and checked.
A key aspect is the distance between the components. This information is crucial to ensure that the assembly functions exactly according to the customer’s requirements. Dimensions such as diameter or length can be adjusted afterwards to ensure perfect coordination of the parts. These 3D scans not only allow us to check the overlap of sealing surfaces, but also to precisely evaluate the position of the components in relation to each other. Another important aspect is the ability to measure concealed distances, which simply cannot be achieved with other (tactile) methods. Optical measuring devices such as our scanning process provide a far greater amount of information and thus enable a more comprehensive inspection. This opens up opportunities for quality assurance at an even deeper level.
With our optical measurement service, we offer companies a powerful tool to ensure that their products meet the highest standards. This technology has the potential to revolutionize the way we test assemblies and take the quality of our products to a whole new level.